Novel strategy exploits a vexing challenge to capture valuable chemicals from hard-to-process part of plants
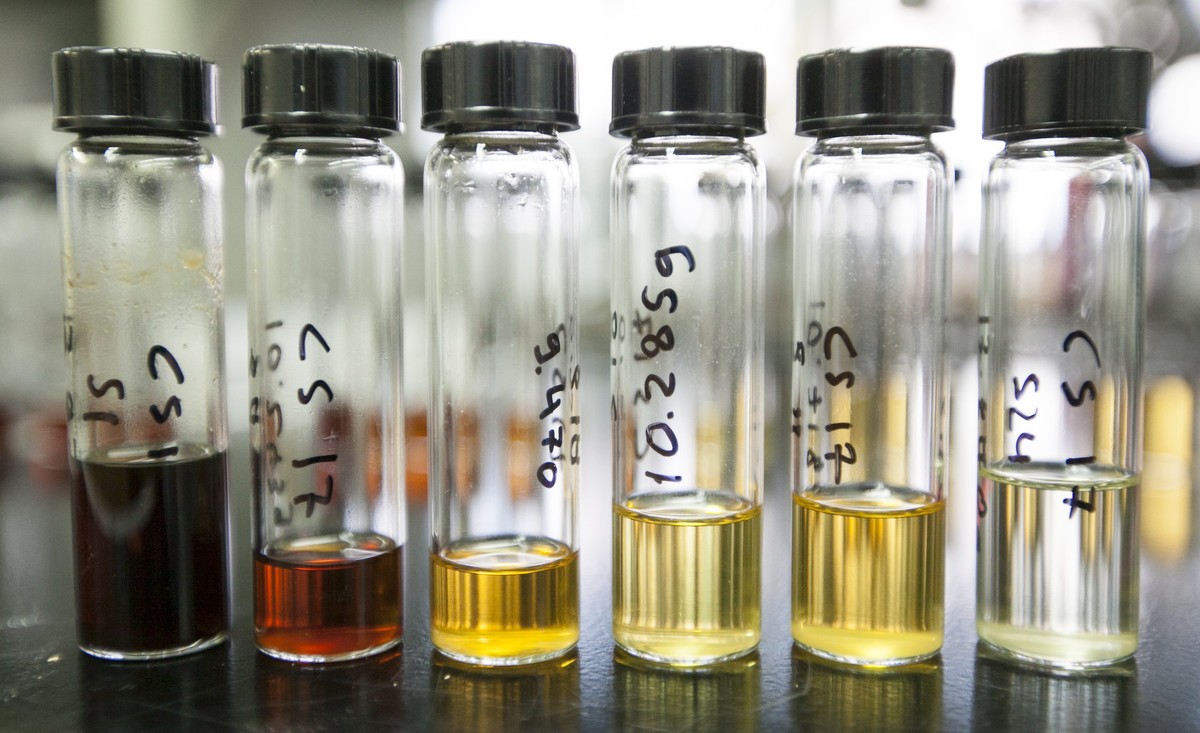
A team of scientists led by a University of Wisconsin–Madison graduate in collaboration with two faculty members has developed a plant-based alternative to a common but toxic ingredient used to make plastic water bottles and food containers.
The research, published in the journal Nature, details a novel strategy for turning a plant biomass historically treated as waste into bisphenols, a class of chemicals used to make plastics and resins.
If successful at an industrial scale, the technology could help replace toxic petrochemicals such as BPA while also generating new revenue streams to make cellulosic biofuel as cheap as fossil fuels.
“This can be used to replace petrol-based bisphenol for polymers like epoxy resin and polycarbonate with comparable properties,” said Xuejun Pan, a professor of biological systems engineering who contributed to the study.
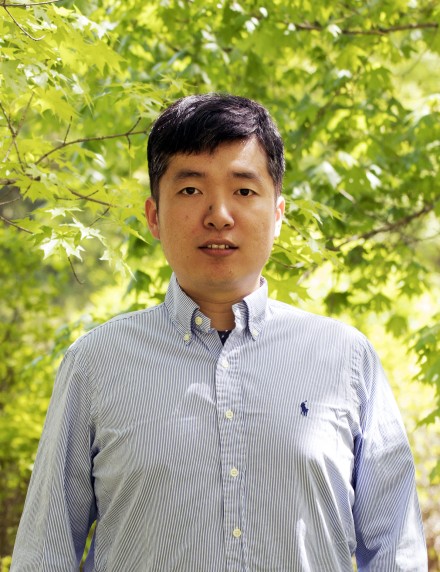
Led by Ning Li, a scientist with China’s Dalian National Laboratory for Clean Energy, the study includes work by more than a dozen scholars from around the world, including Pan and UW–Madison biochemistry professor John Ralph, a researcher with the Wisconsin Energy Institute.
Li, who earned a PhD in 2018 from UW–Madison in biological systems engineering, took on a problem that has long vexed biofuel researchers: how to get value from lignin, one of the three main components of plant biomass.
Lignin is a complex chain of molecules – or polymer – that binds together plant sugars (cellulose and hemicellulose) and provides structural support. As the largest natural source of aromatic (ringed) compounds it would be an obvious source of renewable chemicals and replacements for fossil fuels.
The challenge is to separate lignin from the sugars in a way that doesn’t wreck it.
Deconstructing lignin requires breaking chemical bonds, which is usually done with acid or base at high temperatures. But under those conditions, carbon atoms tend to form new bonds, a reaction known as condensation.
The result is a tangled chemical mess that can’t be broken apart into useful components.

In the past decade scientists conceived a “lignin first” approach that sought to separate lignin in a more usable form. Such approaches have mostly focused on preventing condensation.
Li had another idea: What if we instead exploit condensation to our advantage?
Li found that phenols — a group of aromatic compounds used in products such as disinfectants and vanilla extract — can selectively trap the reactive molecules, preventing uncontrolled cross-linking. This results in a modified form of lignin that can be more easily converted into valuable products.
In this case, the researchers used lignin-derived phenols to modify the lignin, and then they broke it apart using a catalyst — a substance that speeds up reactions without being consumed — to produce bisphenols.
Petroleum-derived bisphenols are widely used in plastic water bottles, epoxy resin coatings, dental sealants, and receipt paper.
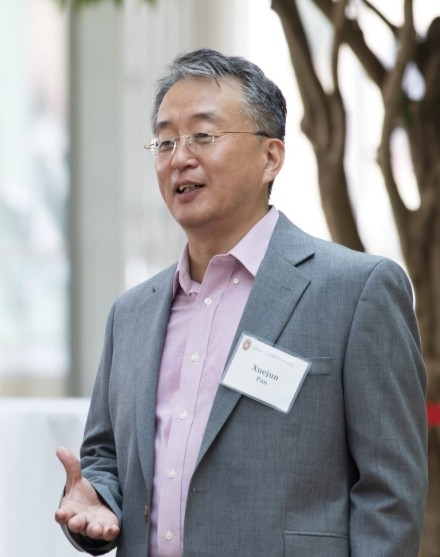
The most well-known, bisphenol A (BPA), mimics the hormone estrogen and has been linked to a wide range of health problems in humans and animals. Common replacements (including BPS and BPF) may be just as harmful.
“They are estrogenics that are wreaking havoc on animals and probably us,” Ralph said.
The lignin-derived bisphenols have the same backbone structure, so they’re good for making polymers, but the addition of an extra chemical group provided by nature makes them benign. Tests conducted by Chinese toxicologists showed a 110-fold reduction in estrogenic effects compared to fossil-based BPA and BPF.
The idea was hatched during Li’s graduate studies in Pan lab, when he led an investigation into a way to avoid lignin condensation during dissolving plant sugars in an acidic saltwater solution. This method apparently left the lignin in a more solid state, limiting the ability of different molecules to react with one another for condensation.
To verify that was the case, the researchers added a phenol to Douglas fir treated with the saltwater solution. The results showed that the small, mobile phenol molecule readily bonded with carbon in the lignin, whereas in the samples without the phenol, the larger lignin polymers showed limited condensation.
It was only later that Li had the idea that phenols could be used to turn lignin into something valuable.
“At that time, we just (saw) this phenomenon, but we didn't realize how important it (was),” Li said.
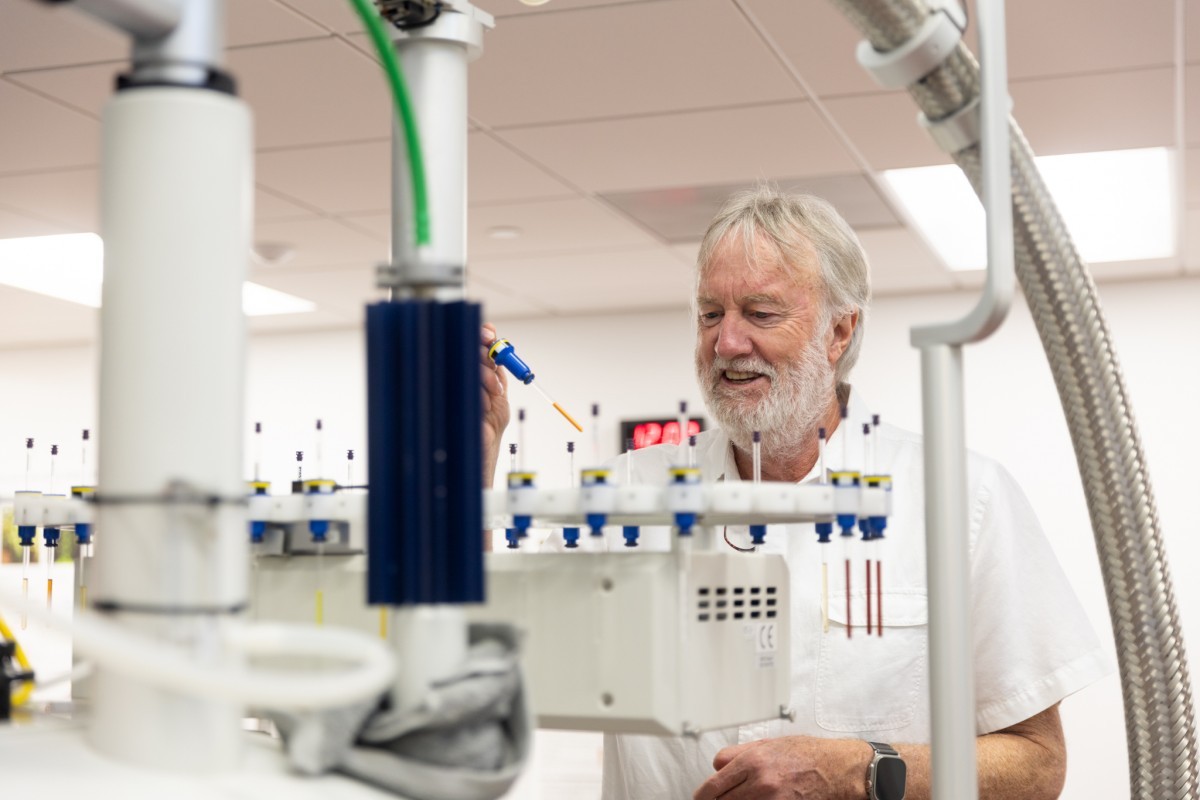
Li, who continued studying the condensation phenomenon after leaving UW–Madison, says the discovery is a “very important step to achieving lignin valorization,” but now his team is working to make the technology feasible at an industrial scale.
There is one other hurdle: currently the only economically viable source of phenols is fossil fuels.
“For short term commercialization – two to three years – it's impossible to get a phenol from lignin as cheap as fossil-based phenols to do this process,” Li said. “So we lose some sustainability for now, but we are confident we can devise more sustainable alternatives in the near future”
Regardless of the source, Ralph said the new method provides another technique for producing clean sugar streams that could be converted to biofuels while also making “a lovely isolable lignin that is useful along with a benign promising BPA replacement.”
“It’s not quite perfect,” Ralph said. “But then what is?”