Department of Energy awards $4 million grant to fund project aimed at demonstrating technology in a way that benefits marginalized communities

A team led by University of Wisconsin–Madison scholars has a plan to turn paper mill waste into plant-based plastics, slashing greenhouse gas emissions and other pollution and creating economic opportunities in ways that benefit marginalized communities.
The U.S. Department of Energy (DOE) has awarded $4 million to fund a collaboration between Wisconsin Energy Institute researchers, the National Renewable Energy Laboratory (NREL) and industry partners. The work will leverage contributions from experts in chemistry, engineering, public policy, and the arts.
The goal is to turn a fibrous plant material called lignin into nylon – used to make textiles, carpets, and molded plastic – for roughly the same cost as petrochemicals but with only a fraction of the pollution that causes climate change.

If successful, the project will demonstrate the commercial viability of a lab-tested process that could be key to developing sustainable alternatives to fossil fuels and petrochemicals, said Shannon Stahl, a UW–Madison professor of chemistry who is leading the project.
“If you're really going to replace petroleum with bio-based feedstocks, everything from plants has to be turned into value,” Stahl said. “The approach must be like petrochemicals, where everything from crude oil is turned into something of value. The goal is to adapt the petrochemical model to a biochemical context.”
But the project aims to go far beyond the engineering challenges by incorporating a plan to collaborate with communities disproportionately affected by pollution, climate change, and economic hardship.
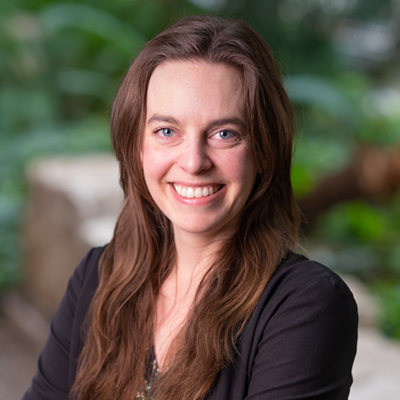
Morgan Edwards, professor of public policy and leader of the Climate Action Lab, will work with researchers at NREL to develop screening tools to guide the siting of biomass processing facilities in ways that ensure equitable distribution of both the benefits and burdens of energy infrastructure.
“With this project, we have a new opportunity to center equity and community benefits early in the technology development process,” Edwards said. “We are designing interactive tools to quantify the direct benefits here in Wisconsin and throughout the U.S. and creating a blueprint for actively involving communities in identifying pilot sites for new, low-carbon products and infrastructure.”
In addition, art professor Darcy Padilla will photograph the scientists, communities, and environments connected to the project.
Padilla, who has documented the impacts of a coal-fired power plant on Native American communities in Arizona and hydraulic fracking in North Dakota, said she is eager to work at the intersection of climate change, science, and one of Wisconsin’s core industries, which has seen more than a dozen mill closures over the past three decades, wiping out more than 21,000 jobs.
“Science is made by people, and it affects people,” Padilla said. “It's usually the affected community that I'm looking at. With this project, it's intriguing to see different facets at different places – to see it from a science perspective, to see where communities are right now, the possible impact on communities.”
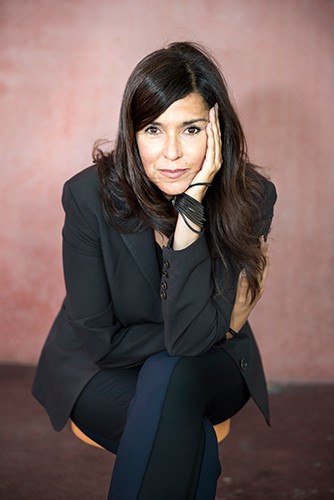
The grant is one of five awarded by DOE’s Bioenergy Technologies Office as part of an initiative to advance the production of affordable biofuels and biochemicals that can reduce greenhouse gas emissions and help slow climate change.
According to DOE, developing such sustainable feedstock and conversion technologies will support the Biden administration’s goal to decarbonize the aviation sector by producing enough sustainable aviation fuels to meet all industry demands by 2050.
While there are industries built around turning plant sugars into products like paper and biofuels, researchers have struggled to find uses for lignin, a complex substance that helps bind those sugars together and make plants strong.
The most abundant biological source of aromatic compounds, lignin could provide an alternative to petroleum-derived chemicals like benzene, toluene, and xylenes that serve as building blocks for plastics, biofuels, and solvents as well as drugs and food additives.
But the irregular structure makes it difficult to break lignin down into useful components. As a result, most pulp and paper mills simply burn it for heat and power, requiring expensive equipment and polluting the air.
Researchers hope to solve this problem with a process developed by NREL that uses genetically-engineered microbes to convert different lignin-derived aromatics into a single product.

Key to doing that at industrial scale are a pair of UW–Madison innovations. One uses air to break apart lignin in a way that produces oxygenated aromatics, which are more water soluble than oils derived through other methods. The other is a method for separating single molecules from chains known as oligomers.
Those target molecules can then be fed to genetically modified bacteria that produce muconic acid. Adding hydrogen turns muconic acid into adipic acid, one of two ingredients used to make nylon-6,6, a tough but elastic material used in things like carpeting, luggage, and airbags as well as car parts and other molded plastics.
Petroleum-based adipic acid is one of the most energy and greenhouse gas-intensive chemicals being manufactured, and the process produces other harmful air pollutants, which Stahl says makes it an ideal target for a plant-based alternative.
And finding new uses for lignin would reduce local air pollution caused by burning it.
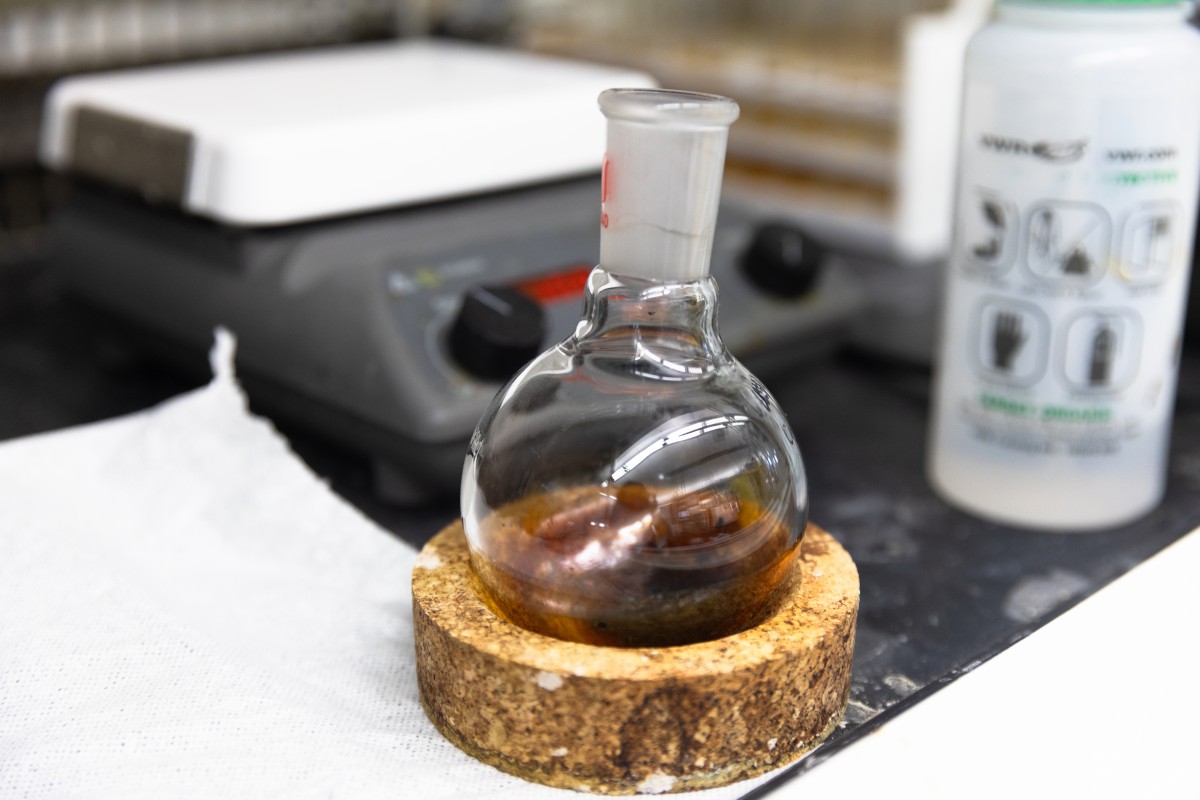
Chelsea Mammot/Wisconsin Energy Institute
Using techno-economic analysis and a life-cycle assessment, the researchers predict they can produce adipic acid at roughly the same cost as the petrochemicals while reducing greenhouse gas emissions by more than 70%.
The team aims to deliver 10 kilograms of lignin-derived adipic acid to a manufacturer to see how the biobased product compares to petroleum-based nylon.
“The main project question we are trying to address in this project is can we compete with existing processes – on a cost basis or on a product purity basis?” Stahl said. “At a molecular level, adipic acid is adipic acid, but each process can generate different byproducts.”
If successful, Stahl said the process could be adapted to produce replacements for other petrochemicals.
“Adipic acid is going to be the showcase for this application, because we have bacteria that can make the precursor,” Stahl said. “But there are many different ways to hijack the machinery of microbes to make new molecules.”