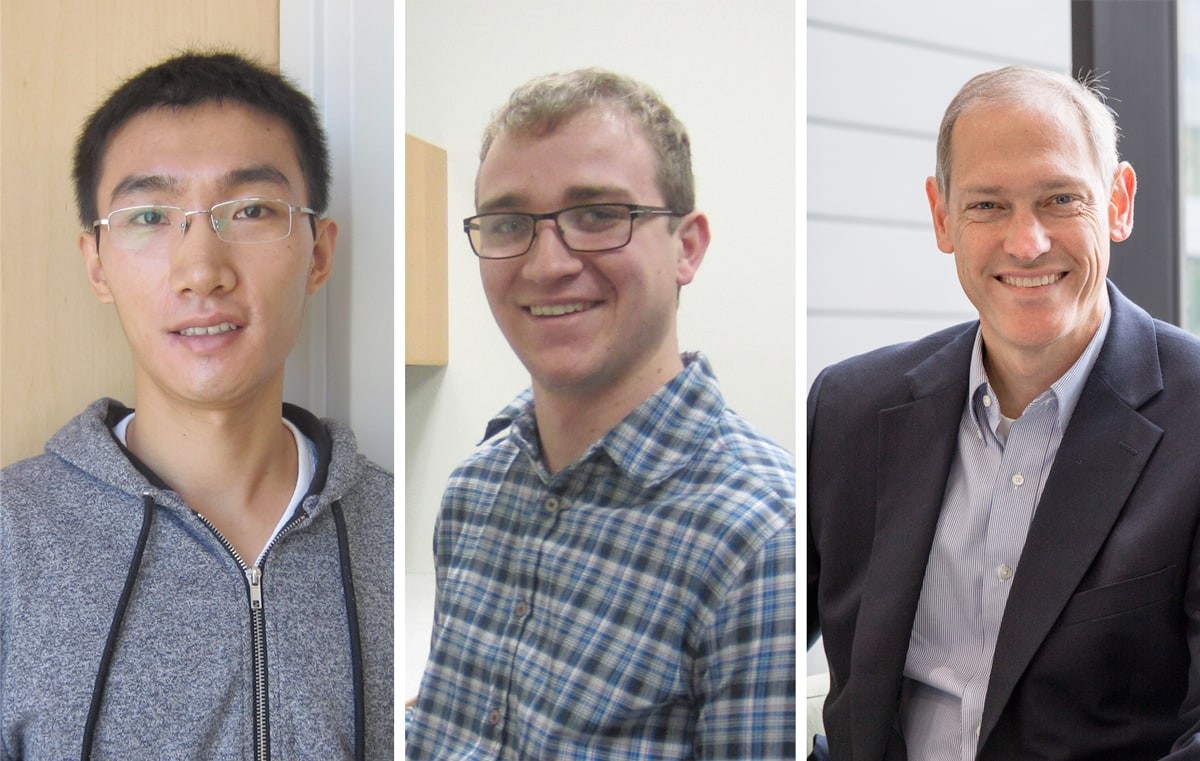
Breaking down plant material for biofuels processing has always required multiple steps, especially when it comes to dealing with the tough, complex polymer lignin. Current methods use a multi-step pretreatment process that focuses on extracting sugars to ferment into fuels. These steps leave behind the lignin, which is typically burned for energy. Ideally, though, lignin could serve as a feedstock for industrial chemicals that make their way into everyday consumer products.
Chemists at the Great Lakes Bioenergy Research Center (GLBRC) have developed a new technology that converts biomass into both carbohydrates and lignin-derived aromatic monomers in a single step. The team, based at the University of Wisconsin–Madison, published the work online September 9 in the Journal of the American Chemical Society.
The new process streamlines the conversion of raw plant material into two value-added product streams: sugars for biofuel production and aromatic compounds for manufacturing and other industrial applications. Fewer steps should also reduce processing costs.
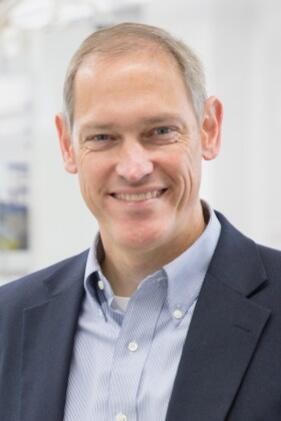
“What we're doing is essentially a direct, one-step generation of carbohydrates and aromatics all in one,” says Shannon Stahl, a professor of chemistry at UW–Madison and co-investigator at GLBRC who led the work.
In addition to requiring additional steps to break down lignin into monomers, current methods also damage the lignin structure, resulting in a lower yield of aromatic molecules. The new approach keeps the lignin in its native state, leaving it more amenable to conversion into monomers and resulting in better yields.
“It’s a double win,” Stahl explains. “You limit the number of operations in the process, which the engineers like, and you also get an improved aromatic monomer yield because you don't have the lignin damage that occurs in that isolation of carbohydrates.
The new method breaks down biomass in the presence of oxygen gas. The resulting oxygenated aromatic monomers are complementary to those produced via current processes that use hydrogen gas. The oxygen-containing products are especially well-suited for chemical applications. Their enhanced water solubility allows for easier integration with other downstream processing methods, such as microbial funneling strategies that turn chemical mixtures into single compounds.
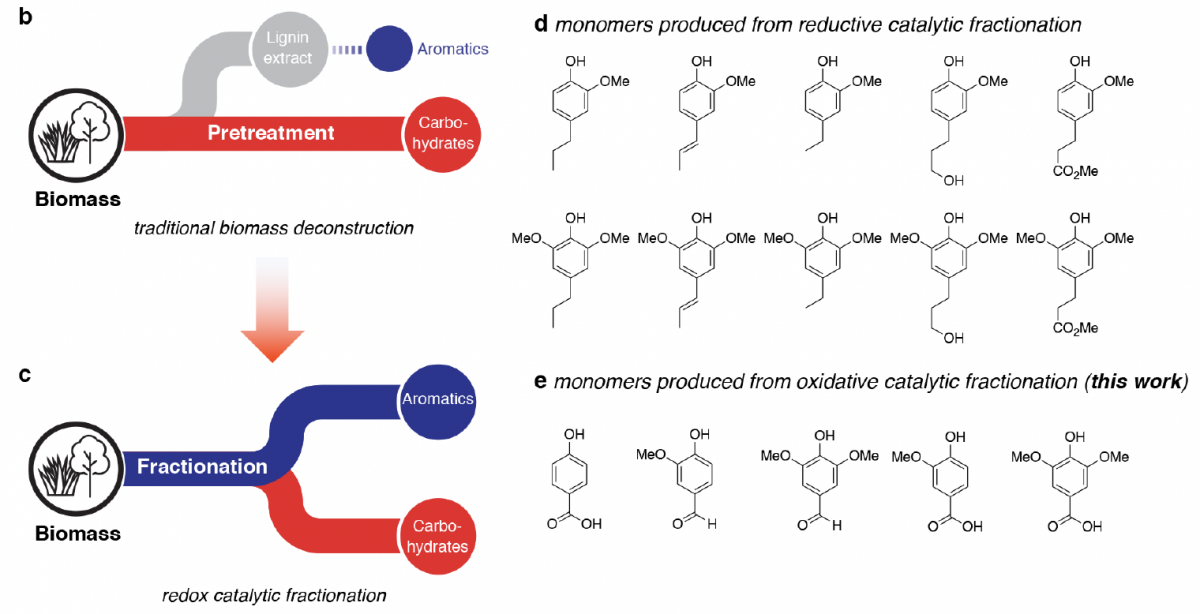
The team recognized that an oxidative process would afford a different suite of chemicals with greater potential value and was motivated to explore whether such a process was possible. Stahl says it’s a way of rethinking biomass processing to consider lignin as a useful product stream on par with carbohydrates, rather than relegating it to a secondary or waste stream.
“In one step, we can access compounds that previously required three or more steps. So, it's really appealing from that perspective,” he says.
Other authors on the paper are Hao Luo, Eric P. Weeda, Manar Alherech, Colin W. Anson, Steven D. Karlen, Yanbin Cui, and Cliff E. Foster.