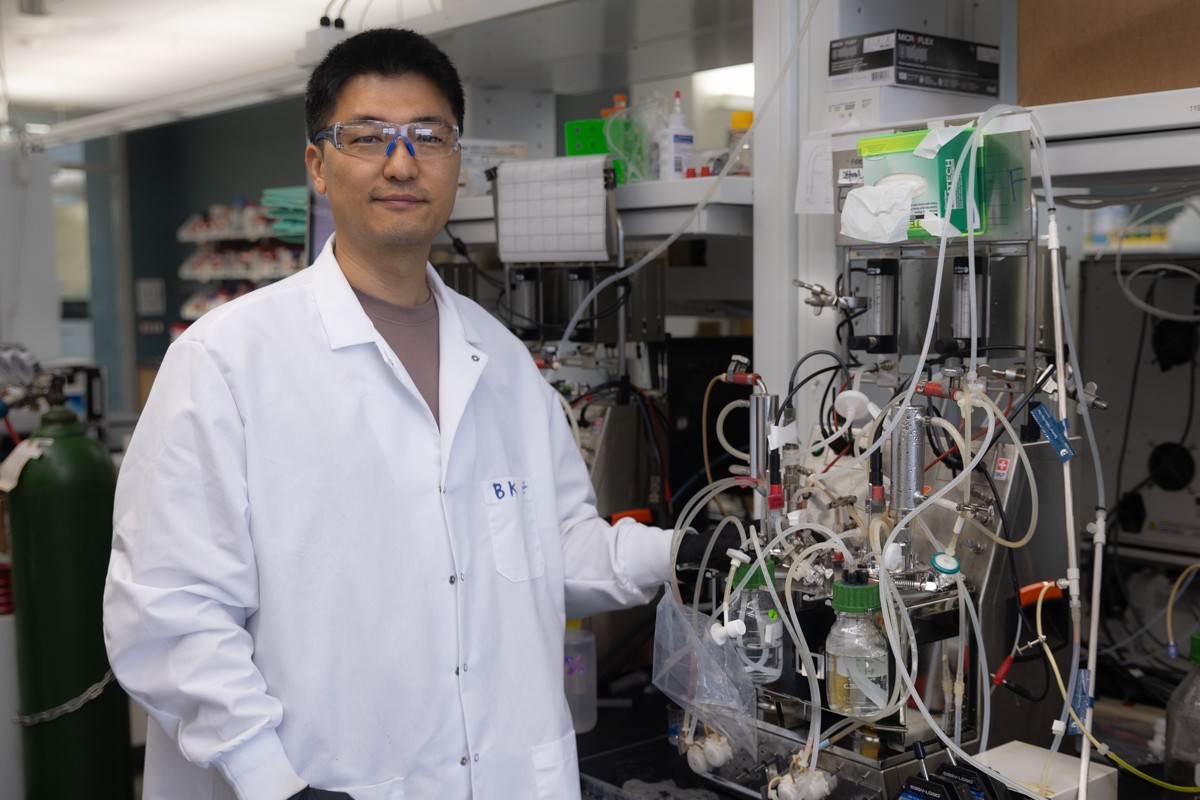
The Science
Lignocellulosic biomass, the woody parts of plants, is made of two types of sugars bound together by lignin. Lignin contains ring-shaped compounds known as aromatics that can be a source of valuable products traditionally derived from fossil fuels, but it's hard to pull these individual chemicals out of the mix. Some bacteria can convert plant-based aromatics into chemicals used to make plastics, but there are challenges to getting high yields.
The Impact
Lignocellulose is the world's biggest renewable resource. The sugars in lignocellulose can be converted into biofuels. To make biofuels as cheap as fossil fuels, biorefineries will need to make valuable chemicals from lignin, just as traditional refineries do with crude oil.
Summary
Scientists with the Great Lakes Bioenergy Research Center tested strategies to increase productivity of a type of dicarboxylic acid, 2-pyrone-4,6-dicarboxylic acid (PDC), from solutions of aromatics derived from treated poplar wood using a genetically modified strain of the bacterium Novosphingobium aromaticivorans in a bioreactor that uses a membrane to separate the product while recycling the bacterial cells.
Shortened retention time, hollow-fiber membranes, and ammonium hydroxide (NH4OH) to reduce acidity contributed to a roughly 14% increase over the highest previously reported PDC productivity from aromatics. Results revealed a trade-off between maximizing high productivity or product titer in the MBR system.