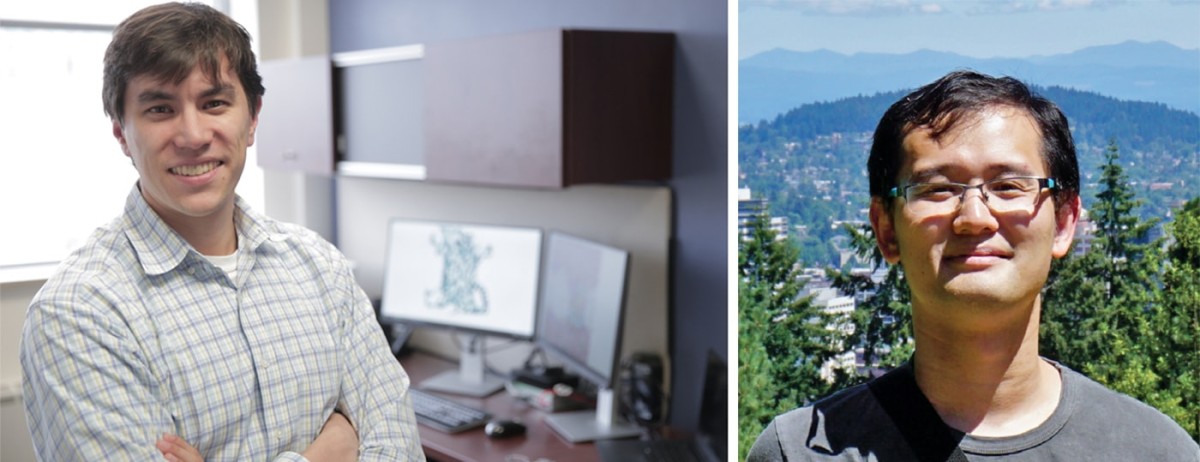
One of the slowest and most expensive steps in turning biomass into chemicals and other useful products is separating the compounds of interest from the mixture of liquid solvents and other byproducts made during processing. In a recent paper, GLBRC researcher Reid Van Lehn describes a computational approach to quickly select solvent systems to extract specific products in high yields, just by inputting the target products’ chemical structures.
In the paper, published in March in Industrial & Chemical Engineering Research, Van Lehn and Zhizhang Shen demonstrate the approach to optimize the isolation of desired lignin monomers after standard depolymerization methods. But the conductor-like screening model for real solvents (COSMO-RS) method can be applied to any liquid-phase product mixtures, they say.

Here, Van Lehn describes the main elements of the method and how it fits into the framework of the GLBRC.
What's one thing you want other GLBRC researchers to know about this work?
This work shows that our molecular modeling tools can quickly predict the thermodynamic properties needed to screen solvent mixtures for liquid-phase separations, which we can use to design solvent systems to extract biomass-derived products.
What challenge are you working to address?
The type of separation process that we explore in this work is liquid-liquid extraction. The idea is very simple: You have an initial mixture of products in solution, then ask what other solvent system you could expose the solution to that would drive the products to naturally migrate into it in such a way that they can be recovered in high purity. Then you can evaporate off that other solvent. What's nice about this approach is it's a very scalable method for separations, and it's potentially cost-effective depending on how you can recycle the solvents.
How might this be applied to bioenergy research?
For lignin, liquid-phase separations are particularly important because the catalytic processes that produce lignin products lead to a product mixture and the reactions occur in solution, so we need ways of separating individual products for further use. Shannon Stahl's group has been investigating these types of liquid-liquid separations using a process called counter current chromatography to separate lignin products, so we hope our method can help guide similar efforts.

What can your computational method do?
We want to separate these products. The challenge with any solvent-based separation method is, what extracting solvent do I choose? If I'm an experimentalist, I can just go buy every solvent I can think of, try them all and see what works. But that's a very time-consuming effort.
We were trying to develop computational methods whereby from knowledge of the thermodynamics of product-solvent interactions we could predict a priori and very rapidly what solvents should be selected. So that's basically what this paper shows: Computational methods to very quickly—on the order of minutes—select solvents that we expect to be able to extract specific products in high yields. In this particular paper we focus on lignin product mixtures, but in principle we could apply this to any range of products and product mixtures in a liquid phase.
What kind of information do you need to input into the model?
The main input is the chemical structure. We take multiple chemical structures at a time to be the multiple possible products. The output is thermodynamic information related to separations. What we don't predict is kinetics—ligand-receptor binding and things related to biology. We have separate methods for that. This method basically produces thermodynamic data, but rapidly and in a chemically specific way.
Where does this work fit into the framework of the GLBRC?
A key question that we want to know in GLBRC is whether a process such as lignin valorization can be made economically viable. Separation contributes significantly to process economics based on prior technoeconomic analysis. Christos Maravelias’ computations in this area are based on choosing an optimal route given many possible variables, such as the method used for separations. The computational method described in this work runs quickly enough that it can plug directly into those process modeling frameworks so that in principle a technoeconomic analysis can evaluate not just whether to do a liquid-liquid extraction, but what is the most cost-effective liquid extraction to do. One can imagine a solvent mixture that does the best job of getting high yield of a product but that uses expensive solvents, and a cheaper solvent with lower separation efficiency but that yields a more cost-effective process overall. Those are the types of questions that we'll be able to answer using this type of computational screening.
One of the Keegstra Fellows will be combining molecular modeling and process modeling, so we’ll be able to develop a more general computational framework with Christos' group. We would also be interested in hearing from others in the GLBRC who could benefit from this combination of modeling techniques—the more people within GLBRC who want to use it, the better!
Read more
Explore this topic further in our research highlight: https://www.glbrc.org/research/highlights/using-modeling-determine-best-solvents-lignin-product-separations
Reference
Shen, Z. and Van Lehn, R. C. “Solvent selection for the separation of lignin-derived monomers using the conductor-like screening model for real solvents.” Industrial & Engineering Chemistry Research 59, 7755-7764 (2020). doi: 10.1021/acs.iecr.9b06086