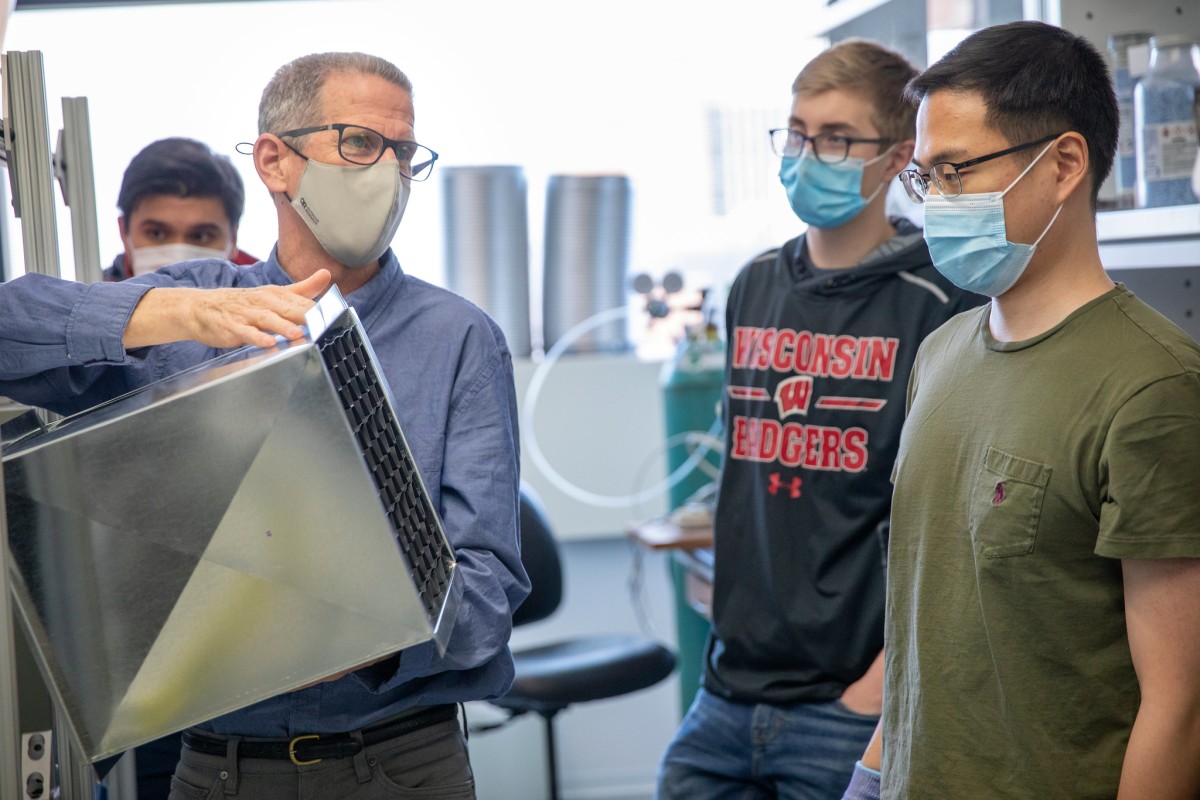
Researchers from the University of Wisconsin–Madison, Penn State, and the University of Illinois Chicago will use a $2.3 million grant from the Department of Energy (DOE) to develop a carbon-negative replacement for portland cement, turning the widely-used and previously carbon-intensive building material into a carbon sink.
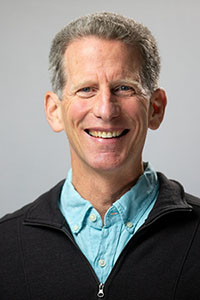
Led by UW–Madison’s Rob Anex, a professor of biological systems engineering in the College of Agricultural and Life Sciences, and, Bu Wang, an assistant professor of civil and environmental engineering in the College of Engineering, the project will use carbon captured from the air to convert industrial mineral wastes like coal ash into a recyclable replacement for portland cement. The end goal is a durable and versatile building material that permanently stores carbon dioxide through a process that pulls more carbon out of the air than is emitted.
The research project is funded through DOE’s Advanced Research Projects Agency-Energy (ARPA-E) HESTIA program which supports the development of new technologies that cancel out the carbon footprint of construction materials while transforming buildings into net carbon storage structures. Research for the project will be conducted in Anex and Wang’s joint lab in the Wisconsin Energy Institute.
Here, we sit down with Wang and Anex to learn more about the project:
What is the challenge in producing portland cement, one of the most common building materials in the world, in an environmentally friendly way?
Wang: We use a lot of concrete and cement in our buildings and roads. The most critical challenge is producing quality concrete that meets all the specifications and requirements of portland cement—it must be strong enough, durable enough, and can be cast in place, while still maintaining carbon negativity.
Anex: In fact, we're trying to make something that's better than portland cement—cement that is more resistant to chloride and more durable.
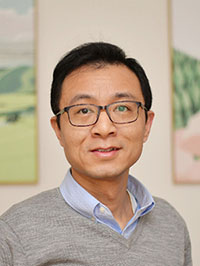
How will this grant help to advance your research in this area?
Anex: There are a bunch of tasks involved here. One is modifying the direct air capture process to create the right quality of carbonated residue. Another task is creating tools for doing high throughput screening so we can test a lot of different feedstocks and combinations of process conditions. We must be able to handle the variability of feedstock and still produce a consistently high-quality product. Then we start creating the recipes for a portland cement replacement and testing it at a larger scale to ensure our product can do all the things that cement has to do.
Wang: In the end, we want to have a new procedure that will accelerate this development cycle.
What makes you most excited about this research?
Anex: Our direct air capture technology is a great for pulling a bunch of carbon out of the air with low energy and low cost. This project will not only reduce our carbon footprint by replacing portland cement but will make the capture process more economical. There is a federal policy that says if you want to sell concrete to the federal government, you must sell them low-carbon concrete, so there is already a market for carbon negative cement. This means we can capture a lot of carbon and produce a valuable product that that will actually pay for that carbon capture.
Wang: I think this is an immediate market opportunity to commercialize direct air capture technologies, and we have one that can really make a fundamental change in how we make cement and concrete. People have been trying to do that for a long time, but I think we're on the verge of a real change.