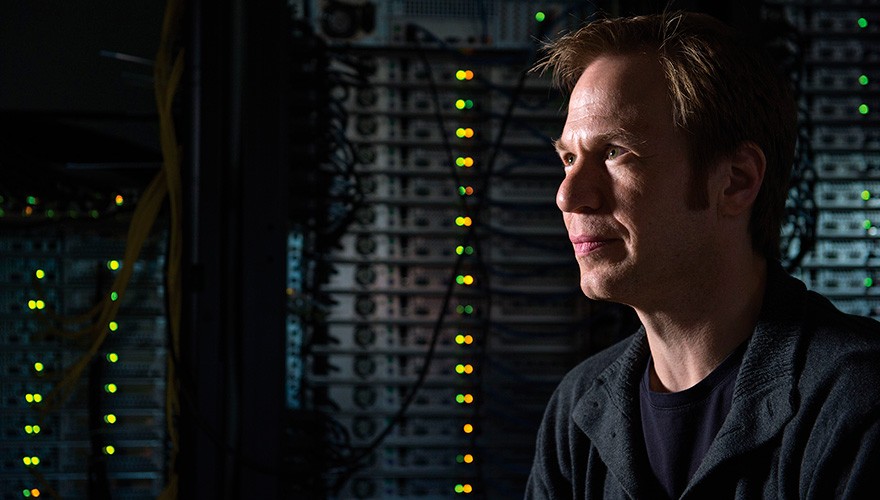
In the United States, the start of 2014 marked the end of an era—the “death” of incandescent light bulbs. Not that all 40- and 60-watt incandescent light bulbs simultaneously stopped working on January 1, 2014, but their manufacture in the U.S. was banned for not meeting stricter energy-efficiency standards. This move follows similar initiatives being put in place around the world since 2004.
With a 135-year history, the incandescent light bulb was worked on, refined and improved by many great minds, inventors and scientists, and, most notably, popularized by Thomas Edison in 1879.
According to the Smithsonian Institute, Edison and fellow researchers tested nearly 1,600 different materials in a long, and ultimately fruitful, quest to find a long-lasting, cheap filament for light bulbs. They eventually decided on carbonized bamboo, after testing materials from coconut fiber to beard hair.
It’s the ultimate story of scientific discovery, isn’t it? An idea followed by trial and error, followed by more ideas and more trial and error. However, it may be a slightly romanticized version of how science works, at least today. The mad genius struck by otherworldly inspiration working tirelessly toward a solution for the problem that plagues their mind is being replaced by computers—and it’s helping speed innovation.
Dane Morgan, professor in materials science and engineering, believes that wasn’t exactly the case then and, with the advent of computer modeling, certainly isn’t the case today.
“People like to say ‘trial and error,’ but that’s almost never really how science approaches new materials. Very few people are just taking completely random guesses,” says Morgan. “Often times, before computers, you’d have people building physical models based on knowledge of simple properties—atomic size, mass, etc.—and their own intuition from past experience.”
It took scientists years and years of refinement and experimentation with existing materials before Edison’s research group found the filament that helped produce long-lasting and cheap light bulbs. This process hasn’t changed that much for the scientists of today, as they search for new materials to make more durable smartphone screens, cheaper solar panels or better batteries.
Look around you, wherever you are, and what do you see? If you’re in an office building there are chairs, computers, windows. Outside of those windows you may see cars, roads, streetlights and other buildings. All of those things are inventions that have made life easier and more convenient. They are also made of materials. We often see the whole of something and without appreciating the parts and materials that make it possible.
“There are so many areas where key enabling material technologies are somewhat hidden, like the materials to make advanced drill bits for accessing new fossil fuel reserves or the material components that have helped make solar energy competitive with other sources in the United States,” says Morgan. “These materials aren’t always getting a lot of press, but they are essential. And the need for these materials is why material science is also essential.”
The power of computer modeling and simulation has increased 100,000 fold since I started doing this kind of research and that pace hasn’t slowed at all. There’s a lot of materials data out there and we are generating it at an ever increasing rate.
Dane Morgan
Morgan’s lab computationally models materials at the molecular level using techniques that solve equations which, in theory, determine all of the basic properties of a material. The power of this type of work lies in its ability to predict the properties of a material without that material physically needing to exist. The drawback is that this takes an immense amount of computational power – so much so that simulations must be limited to a small amount of atoms, the smallest part of matter, over a short period of time.
Naturally, computational modeling often becomes a collaborative effort between a materials scientist and experimental researcher, where one can validate the other and quicken the pace of progress. Morgan estimates that for some properties his lab can screen more than 1,000 materials a year without having to make a single one of them. Consequentially, this reduces the immense number of materials that require actual experimentation and focuses research efforts more narrowly to materials that are most promising for a given application.
Morgan is also the co-director, along with Tom Kuech, professor in Chemical and Biological Engineering, of the Wisconsin Materials Institute, an organization established to promote and support Materials Genome Initiative (MGI) activities at UW-Madison. MGI was started by the U.S. government to help “discover, manufacture and deploy advanced materials twice as fast, at a fraction of the cost.” The initiative, and the Wisconsin Materials Institute, wants to keep pushing new methods to develop materials to enable new technologies, grow our ability to model materials and integrate these models with experiments, and create new ways to aggregate and mine all of the materials science data that is being generated around the world. So that, for example, if someone decides to test a rechargeable battery material in Wisconsin, someone in California could rapidly access that data.
“I cannot currently go online and do a Google search to access all of the world’s material data. It’s buried in papers, on computers, in labs. But, we can get there,” Morgan says. “And potentially, what we can do scientifically with computers has become sort of terrifying. The power of computer modeling and simulation has increased 100,000 fold since I started doing this kind of research and that pace hasn’t slowed at all. There’s a lot of materials data out there and we are generating it at an ever increasing rate.”
“But, I don’t believe [computer modeling] will ever replace experiments as a necessary part of discovery. What we can do is help advance work at an enormously accelerated rate when it comes to material synthesis, processing and characterization. And that will be transformative.”