Cooling systems in power plants require heat exchangers to carry low-grade energy away from the inner-workings of the electrical generation machinery—and improvements to heat exchanger technology aim to increase energy efficiency.
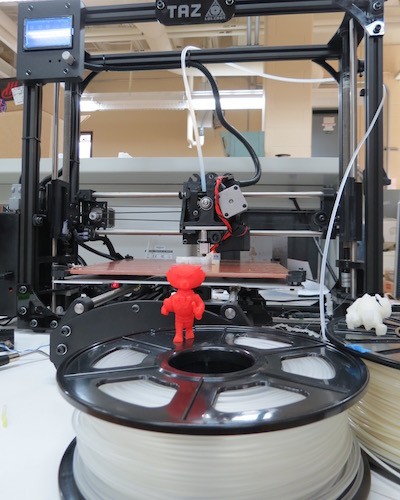
Natalie Rudolph thinks the answer to some of those improvements begins with 3D-printed parts.
The capability of a heat exchanger to transmit energy is determined both by its geometry and the material from which it is manufactured. The metal used to produce conventional heat exchangers transmits heat highly efficiently, but may only be machined in a limited scope of shapes.
When designing a heat exchanger, engineers aim to maximize airflow across the surfaces of the part in order to carry away excess energy. However, the optimum shape for heat transfer may not be feasible for conventional manufacturing. “3D printing allows us to think a little bit differently,” says Rudolph, an assistant professor in the Department of Mechanical Engineering at the University of Wisconsin-Madison and an expert in polymer engineering and 3D printing. “The current generation needs to relearn what is doable with fewer manufacturing restrictions than conventional processes.”
3D printing allows designers to create a spectrum of shapes unencumbered by traditional manufacturing restrictions.
Unfortunately, 3D printing with metal is prohibitively expensive and heat exchangers made from plastic are innately limited due to the material’s poor thermal conductivity.
However, as Rudolph’s colleague Tim Shedd and a group of students demonstrated in their 2014 prototype of a 3D-printed heat exchanger, the freedom in design already allows significant improvements. Rudolph hopes to take it one step further by 3D printing heat exchangers made from plastic polymers blended with a filler material, such as graphene or ceramic, to additionally increase the heat exchange capabilities of the materials.
Rudolph is applying her expertise with polymer blending and additive manufacturing to the project, in collaboration with mechanical engineering colleagues Greg Nellis and Krishnan Suresh, and engineering physics researcher Mark Anderson. Suresh will work to optimize the heat exchanger’s shape, while Anderson and Nellis will model the system’s fluid dynamics to maximize the energy transfer. Together, the researchers hope to produce a prototype heat exchanger within 18 months using a 3D printing technique called fused deposition modeling (FDM). This project is supported by funding from the U.S. Department of Energy ARPA-E program.
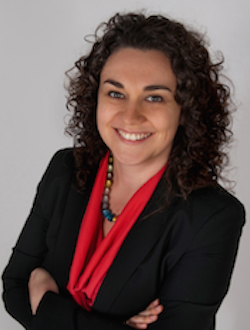
Fused deposition modeling, the technology used both in this project and in commercially available 3D printers, involves feeding polymer filaments of the material to be printed off of a thick spool into a nozzle, or hot end, where it is heated and then deposited one layer at a time. Each of these layers is composed of many small individual parallel filaments roughly the thickness of a human fingernail, giving the finished product a fine layered pattern analogous to the grain of wood. Typically the input material is a cord of plastic, which is an insulator. When a conductive substance is mixed into the input, heat exchangers printed by FDM transfer energy along the lengths of the individual filaments within each layer.
Rudolph sees the innate “grain” in each layer arising from the orientation of the filaments as an opportunity to optimize both the mechanical and thermal properties of FDM-printed heat exchangers. She says that altering the orientation of the deposited layers allows her and her colleagues to tailor the heat conduction properties of individual sections of the part.
FDM historically has been seen as useful for producing prototypes, yet not applicable to large-scale industrial applications. Rudolph, however, says FDM has potential as a manufacturing technology. The low-cost of FDM printers could allow for decentralized industrial production. Rather than manufacturing a part in Madison, for example, and shipping it cross-country to the end user, Rudolph envisions a future where power plants print custom heat exchangers or replacement parts on site to fit the needs of their facility.
To facilitate future large-scale applications of the technology, Rudolph and colleagues have initiated collaboration with Oak Ridge National Laboratory, which recently made headlines by producing a 3D printed car. Rudolph is looking forward to working with researchers there and envisions sending a student to the lab to learn more about industrial systems that are too large for a university setting.
Rudolph is excited about the prospect of this project to improve energy efficiency and reduce water consumption in the United States. Currently, the water used to cool power plants represents the single largest use of fresh water in the United States. Technology for air-cooling power plants is currently expensive and less efficient than water cooling. This project has the potential to effect a change, enabling both improvements in efficiency as well as dramatic reduction in fresh water consumption. Rudolph is enthusiastic about connecting the interdisciplinary dots of fundamental research on fluid dynamics, topology optimization and advanced manufacturing into one application.